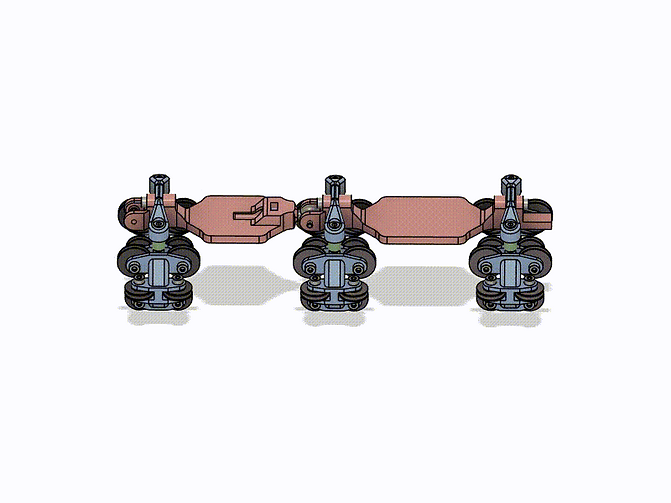
3D Printed Roller Coaster Train, 1:30 Scale, Fusion360
Engineering
From hands-on internships to enriching courses and collaborative club projects, I have immersed myself in a variety of engineering experiences. Explore below to see the skills I've developed and the innovative projects I've been a part of along the way.
Internship Experience
Scenic Engineering and Project Management
Universal Creative Fall 2024
As a scenic engineer Intern, I worked directly on creating and installing large themed elements in Universal's new Super Nintendo World in Orlando, Florida. I facilitated vendor coordination, ensuring that the show set, scenic, and rockwork deliverables of multiple vendors were completed successfully. I worked hands on with the creative team to ensure that scenic elements were up to creative and I.P. standards. Through this, I facilitated change orders between the creative team and vendors, documenting and tracking them throughout their lifecycle.
​
Donkey Kong's Family Hut, pictured right, was a major scenic and rockwork effort which I helped to coordinate.

3D Printed Roller Coaster Project
I began leading a project to design and build a unique, 3D printed model rollercoaster with the Theme Park Engineering and Design Club at Purdue. After leading the project for 3 semester as a design lead and project manager, completing a successful design run and operating our model, I began to work on a person version of the project to act as an educational demonstration. The photos to the right display this group project.
​
Using the lessons from the group effort, this personal project aims to utilize industry leading design for additive manufacturing principles to develop a 1:30 scale, functioning model which can serve as a demonstration of a typical theme park attraction control system. Utilizing SolidWorks, Fusion360, Force Vector Design, and Python in my work, I have successfully test printed a scale model train, track segments, and supports in Selective Laser Sintering (SLS) using Nylon-12. The photos below showcase this personal project.
​
​



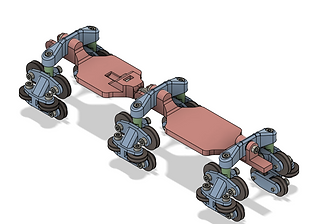

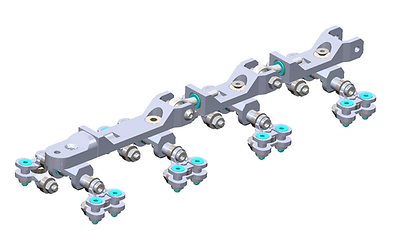
Assistant Technical Direction
Purdue University Department of Theatre
As an Assistant Technical Director for Purdue, I was assigned to deliver on a specific scenic unit for a production of Gloria by Branden Jacobs Jenkins. I was assigned a set of wall flats, including a door, to draw, estimate time required to construct, and craft a cost estimate for. Additionally, I was tasked with creating detailed instructions for load-in install and strike removal from the theatrical space. This exercise was completed in preparation for my senior capstone in the Department of Theatre.

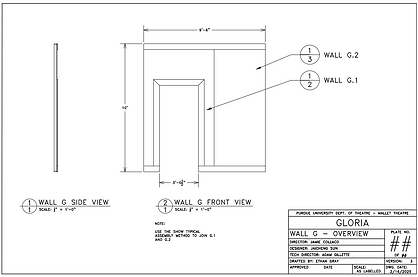

Excerpts from ATD Drawing Packet

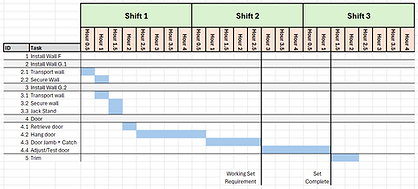
GANTT Chart for Load-In
PERT Time Estimate for Load-In
Coursework
ME 354 Machine Design & THTR 550 Mechanical Design for the Stage
In these courses, I learned how to apply traditional engineering design practices to theatrical design processes and principles, merging my education in engineering with entertainment. In Machine Design, I learned the nuts and bolts of engineering design, including calculations for dynamic and cyclic loading, surface wear, lubrication, and gear design. In Mechanical Design for the Stage, I've applied some of these principles to develop power train mechanisms for unique scenic applications, including a motor drive system for a 25 foot, 4500 pound platform.
​
Related documentation, including FMEA, Bill of Materials, and more for the above THTR 550 project can be seen.


THTR 550 Friction Drive CAD Model
THTR 550 Friction Drive Power Quick Tabulation Sheet

THTR 550 Bill of Materials

THTR 550 FMEA Excerpt
ECE 20007 Introduction to Circuit Design Laboratory
The final project for this course challenged my knowledge in circuit design and implementation. The goal: build a functioning analog audio equalizer.
​
This project utilized analog RC band pass and RCL band reject filters to create the bass, treble, and mid-range channels, each with -3dB cutoffs. These channels could have their gain controlled by three potentiometers to achieve the desired mix. Further, a master volume control potentiometer was added to control the entire device. The equalizer was required to output less than
15 mV(RMS) at minimum power and near 100 mV(RMS) at maximum power. Additionally, the maximum recombined signal could not ripple more than 15 mV(RMS) and the entire device needed to output more than 400 mW of power across all desired frequencies.
ECE 20007 Final Project Audio Equalizer Demonstration
Order: Bass, Mid-Range, Treble, Master Volume


ECE 20007 Audio Equalizer Circuit
Full Report and Circuit Analysis